Optimisation et maîtrise des essais
Comment optimiser le planning de démarrage dans les meilleures conditions de performance et sûreté ?
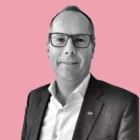
Bruno Pelé
Directeur des Opérations Management de la Construction
Diplômé de l’École Nationale Supérieure des Arts et Industries de Strasbourg, Bruno a intégré Assystem il y a plus de 35 ans en tant qu’Ingénieur d’essais. Impliqué sur de nombreux chantiers nucléaires majeurs, il prend en charge en 2019 le pilotage des activités liées au management de la construction et à la mise en service d’Hinkley Point C au Royaume-Uni. Il dirige désormais ces activités dans le cadre du démarrage du programme EPR2 en France.
Comment optimiser le planning de démarrage dans les meilleures conditions de performance et sûreté ?
La phase d’essais et de mise en service est l’une des étapes clés du management de la construction d’un programme industriel. Faisant suite aux études, à la conception, et à la construction d’une infrastructure, les essais et la mise en service représentent le jalon final avant le passage de relais à l’exploitant, dans des conditions de fonctionnement et de sûreté optimales.
La mise en service d’une installation suppose en effet que celle-ci ait été essayée, contrôlée et vérifiée, pour en garantir la bonne conformité aux exigences de sûreté, de performances et réglementaires : stratégie d’essais, préparation et réalisation des essais, et analyse des résultats sont autant de solutions pour anticiper les écarts aux cahiers des charges et aux exigences de sûreté.
Pour optimiser cette étape clé, il existe désormais des plateformes de test digitalisées, notamment pour le contrôle commande, grâce à des outils de simulation. Ces derniers permettent de gagner en efficacité, de réduire les coûts de mise en service et les risques de régression, ainsi que d’assurer la montée en compétences du personnel d’exploitation.
Optimisation et maîtrise des essais : une étape indispensable pour assurer le « delivery » d’une installation fonctionnelle, robuste et sûre…
Les essais industriels ont un double objectif : d'une part, vérifier et, le cas échéant, diagnostiquer la conformité d'une installation ou d'un équipement aux spécifications ; d'autre part, simuler les performances de l'installation en fonctionnement, afin d'ajuster ses réglages techniques pour garantir un fonctionnement optimal lors de sa mise en service. Une fois les essais réalisés, il faut ensuite s’assurer d’une transition la plus fluide possible avec la fin de la construction en amont, et le transfert à l’exploitant en aval.
La mise en place d’une méthodologie d’essais basée sur une approche fonctionnelle des installations est centrale pour garantir leur mise en service rapide et performante. Il faut effectuer le plus tôt possible ce basculement, d’une logique de marchés en phase de construction vers une logique fonctionnelle pour les essais. Chez Assystem par exemple, notre approche est ainsi basée sur l’anticipation, le démarrage progressif et l’intégration de l’exploitant dès la fin de la construction afin de réaliser une prise en main la plus simple et la plus rapide possible.
Optimiser le planning de démarrage d’une installation passe donc par une maîtrise des essais en plusieurs étapes clés où chaque maillon de la chaîne à son importance : réaliser une cartographie géographique et fonctionnelle de l’installation, assurer la validation chez les fournisseurs (notamment le contrôle commande), prendre le temps et les moyens d’une transmission rigoureuse des installations entre le montage et les essais, et enfin accompagner le support au démarrage progressif des fonctions élémentaires aux fonctions principales afin d’identifier les dysfonctionnements et y remédier au plus vite.
Planification et exécution des tests, évaluation des résultats de la phase de test et de la mise en service, méthodes d'intégration pour l’exploitant, simulation de tests (plateformes I&C), anticipation des essais dans les locaux du fournisseur sont les facteurs clés de succès pour livrer et maintenir une installation performante.
Les équipes d’Assystem ont appliqué cette méthodologie à l’occasion d’une mission de support à la construction et à la mise en service de l’EPR finlandais d’Olkiluoto (OL3). En effet, nos experts y ont assuré le management de projet en matière de contrôle-commande pour les systèmes autonomes de la centrale : validation des documentations techniques du fournisseur et de ses procédures d'essais (matériaux et logiciels de contrôle-commande), suivi de fabrication des cabines et des essais en usine, réalisation des tests d'acceptation en usine, et enfin rédaction des rapports de test de non-conformité. Cet accompagnement tout au long des phases d’essais a ainsi garanti une mise en service de l’EPR dans des conditions de fonctionnement optimal.
Une maîtrise des risques et une garantie de sûreté depuis la mise en service jusqu’au démantèlement de l’installation
Pendant la phase de test, il est important de valider le respect des exigences de conception issues du cahier des charges, ainsi que celles des autorités de sûreté, en démontrant la conformité de toutes les installations et activités avec les spécifications applicables.
Les essais sont une étape clé de la sûreté nucléaire et doivent s’appuyer sur un personnel expérimenté disposant d'une solide expertise pour éviter les écueils courants. Assurer la préparation, la coordination, la supervision des essais et enfin l’analyse approfondie de leurs résultats sont des compétences essentielles pour réduire les risques et prévenir les problèmes de sécurité et de sûreté lors de la mise en exploitation de l’installation.
La phase d’analyse des résultats d’essais est l’une des clés de voute pour démontrer la conformité de tous les systèmes. Le recours à des solutions digitales puissantes, capables d'agréger des quantités considérables de données et de les analyser par rapport aux exigences viennent aujourd’hui compléter l’expertise des ingénieurs d’essais pour l’analyse des éventuelles anomalies.
Dans le secteur nucléaire, les problématiques de sûreté sont centrales et la règlementation de plus en plus stricte s’adapte au contexte et au retour d’expérience. À la suite de l’accident de Fukushima, l’Autorité de Sûreté Nucléaire (ASN) a par exemple émis de nouvelles prescriptions techniques, dont l’une d’elle impose d’équiper la totalité du parc nucléaire français d’une source électrique de secours dite « ultime ». Ces Diesels d’Ultime Secours (DUS) sont installés dans des bâtiments « bunkérisés » au sein des centrales et sont prévus pour résister à tous types d’agressions (séisme, inondation, tornade, attaque…). Les équipes d’Assystem ont ainsi directement contribué à la mise en œuvre de ce nouveau cadre réglementaire, en prenant en charge la supervision des essais de l’ensemble des 56 DUS du parc en exploitation :
Concrètement nos missions consistaient à l’analyse des Procédures d’Exécution d’Essais (PEE), la rédaction des programmes de surveillance, le support au suivi des travaux de montage, la surveillance des essais, l’analyse des Fiches de Non-Conformité (FNC) montage et essais, l’assistance aux chargés de surveillance du client pour les essais d'endurance, le management et la supervision du chantier et des activités logistiques liées aux essais.
Ainsi, l’intervention d’experts essais et mise en service est un prérequis pour la livraison opérationnelle et l’exploitation sûre d’installations complexes. Pour en optimiser l’organisation, le suivi, la qualité, les coûts et les délais, l’ingénierie s’appuie évidemment sur des solutions de plus en plus innovantes grâce au recours au digital.
Des solutions de simulation au service de l’optimisation et la maîtrise des essais
Sur des installations complexes telles que des centrales nucléaires, c’est en effet près de 100 000 signaux électriques qu’il faut pouvoir tester en garantissant la préparation, l’enregistrement et le contrôle de toutes les données associées aux essais.
Une des solutions possibles pour digitaliser les opérations d’essais et de mise en service est le jumeau numérique : en tant que modèle, il offre en effet une réponse concrète aux enjeux d’agilité, d’anticipation, de sûreté et de performance lors des phases de tests et démarrage. Le jumeau numérique va ainsi permettre l’optimisation des essais (réduction du nombre) grâce à la modélisation du séquencement global des essais et des interfaces entre éléments via l'ingénierie système basée sur les modèles (MBSE), la collecte et l’enregistrement des données des tests et essais au sein d’une plateforme digitale en temps réel ou encore la visualisation en temps réel des données par un module d’intelligence artificielle qui compare les résultats des tests et propose des solutions en cas d’écart ou de non-conformité. La modélisation couplée aux données récoltées en temps réel peut également être utile pour créer des scénarios multiples qui, au travers de simulations vont permettre de tester différentes hypothèses et ainsi évaluer le comportement de l’installation lors des phases de tests avant la mise en service.
Dans le cadre de la mise en service d’un EPR, Assystem a par exemple accompagné le développement d’un ensemble d’outils informatiques permettant de digitaliser les phases d’essais et de mise en service, en particulier pour les systèmes I&C (Instrumentation & Control). Nos équipes ont mis à disposition du client une solution digitale dédiée, capable de structurer les différentes campagnes de tests, de gérer les données de tests (tests effectués, tests restants, fiches d'écart), d’enregistrer en temps réel les informations partagées au sein des équipes, ou encore de visualiser et communiquer sur le déroulement des tests à l’aide de fiches d’indicateurs de progression.
Pour les acteurs industriels, les bénéfices de cette digitalisation sont évidents : gain de temps, efficacité et traçabilité, le digital permettant de présenter les données de tests au bon format et au bon moment, amélioration de l'accès aux données à tout moment et en tout lieu sur site, amélioration de la performance des tests et de la productivité des ingénieurs essais, mais aussi amélioration de la sécurité des tests, grâce à la mise en place de processus et procédures pour éviter les pertes de données.
Garants de la livraison d’une installation conforme, opérationnelle et sûre, les essais sont donc une étape stratégique dans le cycle de vie d’une installation complexe et doivent être pris en charge avec la plus grande rigueur. L’expertise et la fiabilité apportées par l’ingénierie et le digital viennent renforcer cette garantie tant d’un point de vue technique que fonctionnel et assurent, par ailleurs, l’intégration optimale et coordonnée des essais avec les autres phases de site, en amont (conception, construction, montage) et en aval (transfert à l’exploitation et maintenance).